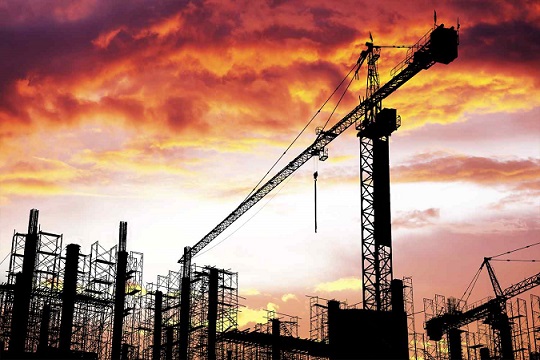
Industrial construction projects are often complex and involve multiple stakeholders, including owners, contractors, architects, and engineers. The success of these projects depends on the efficient coordination and collaboration of all parties involved. However, achieving this can be a challenge, as delays, budget overruns, and other issues can arise. To address these challenges, the construction industry has turned to lean construction techniques. In this article, we’ll explore what lean construction is and how it can help maximize efficiency in industrial construction.
What is Lean Construction?
Lean construction is a philosophy and management approach that emphasizes collaboration, communication, and continuous improvement. It is based on the principles of lean manufacturing, which originated in the automotive industry and was later adopted by other industries, including construction.
At its core, lean construction aims to eliminate waste and optimize processes to improve project efficiency and reduce costs. It involves a systematic approach to project management that emphasizes the following key principles:
- Value: The focus is on delivering value to the customer, which means understanding their needs and expectations and aligning all project activities with those goals.
- Flow: The goal is to create a smooth and continuous flow of work, which means eliminating delays, interruptions, and bottlenecks.
- Pull: The focus is on responding to customer demand in real-time, which means having the right resources, materials, and information available when and where they are needed.
- Perfection: The goal is continuous improvement, which means constantly seeking ways to optimize processes, eliminate waste, and enhance efficiency.
Lean Construction Techniques for Industrial Construction
Now that we’ve covered the basics of lean construction let’s explore some specific techniques that can help maximize efficiency in industrial construction projects.
- Last Planner System (LPS)
The last planner system is a collaborative planning and scheduling approach that involves all stakeholders in the project. It aims to create a realistic and reliable plan that takes into account all factors that could affect the project’s success. The LPS involves the following steps:
- Collaborative planning: All stakeholders work together to create a plan that takes into account each party’s responsibilities, constraints, and timelines.
- Weekly work planning: The team meets weekly to review progress and plan upcoming work. They identify potential issues and make adjustments to the plan as needed.
- Daily huddles: The team meets each day to review progress, identify any obstacles, and plan for the day’s work.
- Retrospectives: The team meets at the end of each phase or milestone to review what worked well and what didn’t. They use this feedback to improve processes for the next phase.
The LPS approach can help improve communication and collaboration between stakeholders, which can reduce delays, rework, and other issues that can affect project efficiency.
2. Building Information Modeling (BIM)
Building Information Modeling is a digital modeling process that involves creating a 3D model of the building and all its components. BIM software allows designers, contractors, and owners to collaborate and coordinate more effectively by sharing information in real-time. BIM can help improve project efficiency by:
- Reducing errors and conflicts: BIM software allows stakeholders to identify and resolve potential conflicts and errors before construction begins, which can reduce rework and delays.
- Streamlining coordination: BIM software allows stakeholders to coordinate activities and materials more efficiently, which can reduce delays and waste.
- Enhancing communication: BIM software allows stakeholders to share information in real-time, which can improve communication and reduce misunderstandings.